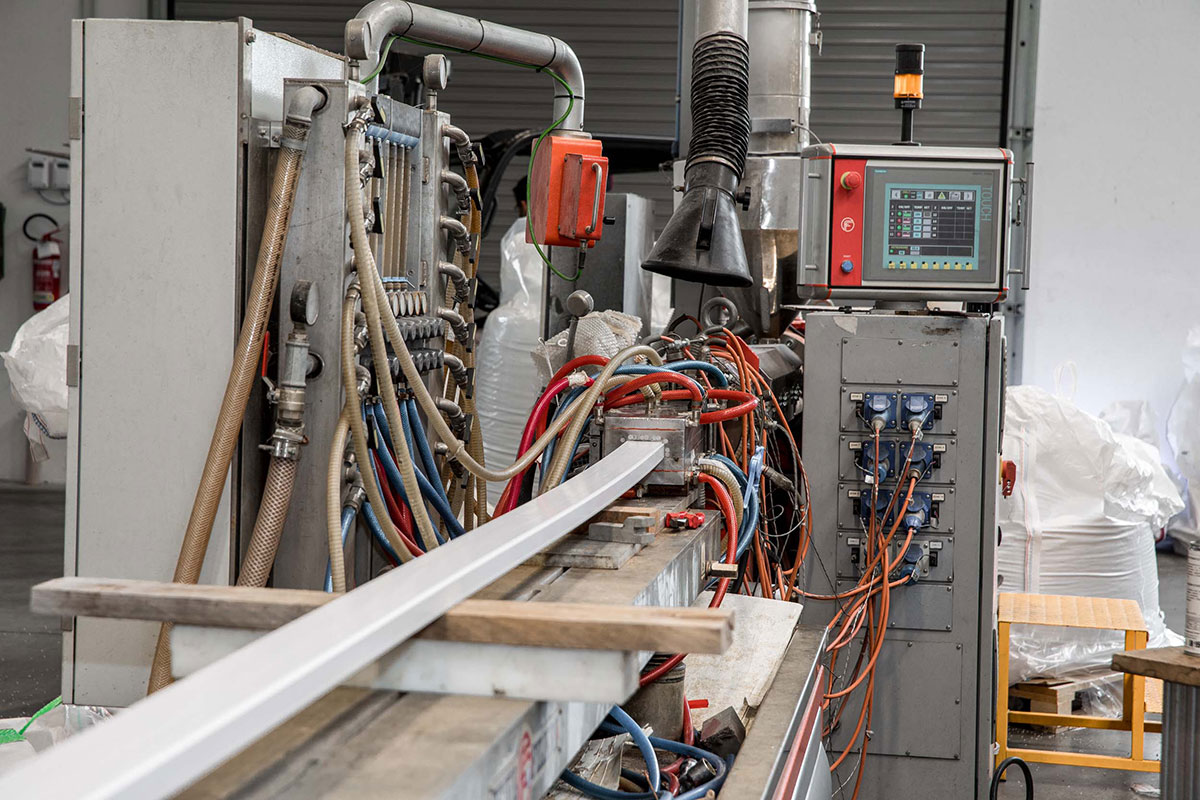
Extruders are essential tools in the process of transforming plastics into finished products. Thanks to these machines, it is possible to produce a wide range of plastic items that meet the needs of our increasingly advanced society. The global extruded plastics market was valued at $185.6 billion in 2020, and is projected to reach $289 billion by 2030.
What is plastic extrusion?
Plastic products can be made by employing different technologies. Extrusion is one of them: it consists in heating the polymer (which usually comes in the form of granules or pellets) to the melting point and passing it through a mold that gives the desired shape. The machine used to carry out this operation is the extruder. This machine, equipped with a rotating screw, pushes the plastic material to let it pass through a die.
Extrusion is a versatile process because it allows the production of a wide range of plastic products: from the simplest parts such as foils, tubes and profiles, to more complex items such as automotive parts and electronic components. Thanks to its versatility and possibility to employ a variety of different polymers, extrusion has played a key role in the development of plastic industry.
Other methods such as injection, compression or transfer molding, blow molding filming, pultrusion or thermoforming processes can be used as alternatives to extrusion.
What is the structure of an extruder and how does it work?
An extruder used to work plastic polymers essentially consists of a cylinder, in which rotate one or two worm screws. The screw acts as a transport and mixing system for the polymer. The heat and friction caused by the rotation melt the plastic material, bringing it into a viscous or liquid state.
As the melted material is pushed towards the extrusion head, it is compressed. The extrusion head shapes the material, giving it a specific shape based on the desired product profile. Once out of the extrusion head, the product is cooled by air or water.
To reduce friction properly, the surface of the screw is polished to make it smoother, while the cylinder surface is treated to become rougher. This prevents the screw from simply rotating around the material without making it advance.
There are two types of plastic extruders:
- Single-screw extruders consist of a single screw. They are generally used for granular plastic materials and allow the production of small products of the same size or large tubes.
- Twin-screw extruders consist of two interlocking screws that can rotate in the same or opposite directions. In section, their shape is similar to a partially overlapping double circle. They are used to produce profiles for window frames, small and large tubes, roofing panels, and profiles of all shapes and sizes. They are also used in the recycling of plastics.
Co-extrusion
Co-extrusion is a process by which two or more materials that are different from each other are simultaneously used to perform the extrusion of a single part. The production process involves multiple extruders to form layered or encapsulated parts. Each extruder provides the precise amount of melted plastic needed for the operation. Five or more plastic materials can also be used in a single cycle.
This technique is used because, when several different plastic materials are combined together, the finished product has distinct properties from those of the individual starting components.
However, not every material is suitable for co-extrusion because some polymers do not combine properly with each other. In some cases, violent reactions may even occur if they are combined together. In addition, plastic materials with significantly different melting temperatures are not compatible with this process.
VBN’s extruders
ZVBN has more than 50 extrusion and co-extrusion systems for plastics processing. This very wide range of tools allows the production of extruded parts of all lengths, with customized cuts from small to large sizes on customer’s request.
In more complex or particularly large and heavy processes, both single-screw and twin-screw extruders are used, consisting of 2 parallel or conical interlocking screws that rotate within the cylinder. Countless types of plastics can be processed and different materials can be extruded simultaneously, coming out coupled from the die.
VBN also has an in-house department for the design and production of custom dies. This solution allows to further customize the extrusion process and produce profiles and tubes of the desired dimensions.